选择铝合金压铸定制作为生产加工方式,在工业制造中具有多方面显著优势,尤其适用于需要复杂结构、批量生产且对性能有特定要求的产品。
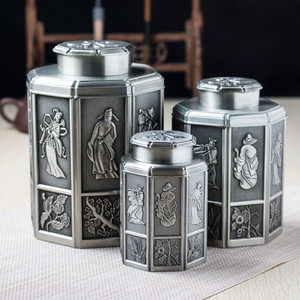
一、工艺特性带来的生产优势
高精度与复杂结构成型能力
压铸工艺可通过模具一次成型复杂几何形状的零件(如带凹槽、筋条、孔位的结构),尺寸精度高(通常可达 IT10-IT12 级),表面粗糙度低(Ra1.6-6.3μm),后续无需大量机械加工即可满足装配需求,减少加工步骤和材料浪费。
例如:汽车发动机缸体、电子设备外壳等复杂部件,可通过压铸一次成型,避免多部件拼接的误差。
高生产效率,适合批量制造
压铸模具使用寿命长(铝合金压铸模具可达数万至数十万次),单次压铸周期短(几秒到几十秒),能快速实现大批量生产,显著降低单位产品的制造成本,尤其适合需求量大的工业产品。
材料利用率高,成本可控
压铸过程中金属液在高压下填充模具,材料损耗少(通常利用率达 90% 以上),相比锻造、机加工等工艺更节省原材料。同时,批量生产可摊薄模具成本,进一步降低综合成本。
二、铝合金材料本身的性能优势
轻量化与高强度结合
铝合金密度仅为钢的 1/3 左右,通过压铸成型后,零件强度、硬度可满足多数工业需求(如抗拉强度可达 200-500MPa),尤其适合对重量敏感的领域(如汽车、航空航天、医疗器械),能减少整体设备能耗或负载。
优异的耐腐蚀与导热性
铝合金天然具备一定的耐腐蚀性,经表面处理(如阳极氧化、电镀)后可进一步提升;同时,其导热性能良好(约为钢的 3 倍),适合需要散热的部件(如 LED 灯具外壳、逆变器壳体、电机端盖)。
良好的表面处理兼容性
铝合金压铸件可通过喷涂、喷砂、拉丝、阳极氧化等多种表面处理工艺,实现多样化的外观效果(如哑光、高光、彩色)和功能强化(如耐磨、绝缘),满足不同行业的审美与性能需求。
三、定制化带来的适配优势
高度贴合产品设计需求
定制化服务可根据客户的图纸或样品,精准匹配产品的尺寸、结构、性能要求,尤其适合非标准件或创新设计产品,避免因通用件适配性差导致的功能缺陷。
一站式解决方案,缩短供应链
专业的压铸定制厂家通常提供 “模具设计 - 压铸成型 - 后续加工(如 CNC 精密加工)- 表面处理” 的一体化服务,客户无需对接多个供应商,简化生产流程,缩短产品研发和交付周期。
灵活性强,支持小批量试产与快速迭代
即使是小批量试产(如几百件),压铸定制也能通过优化模具设计和生产参数实现;对于需要迭代升级的产品,可通过修改模具快速调整结构,适应产品更新需求。
四、适用领域广泛,场景适配性高
铝合金压铸定制几乎覆盖所有工业领域,包括:
汽车工业:发动机零件、变速箱壳体、车门框架等;
电子电器:手机中框、笔记本电脑外壳、充电桩壳体、散热部件;
智能家居:智能门锁外壳、扫地机器人底盘、空调压缩机部件;
新能源领域:充电桩结构件、电池包壳体、光伏支架配件;
医疗器械:轮椅车架、监护仪外壳等(需满足医疗级洁净度要求)。